Blog
Composition description of enamel glaze for glass-lined reactor
Release time:
Nov 19,2021
Information Summary:
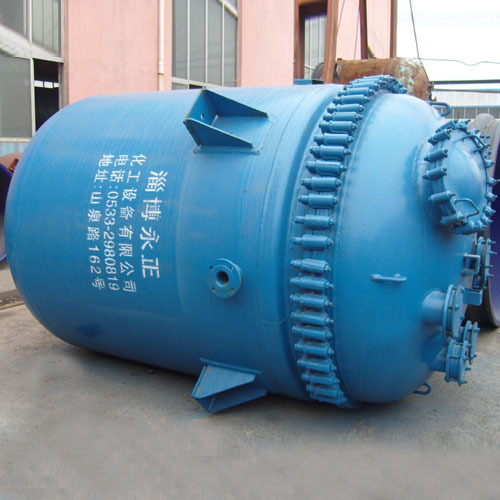
Glass-lined reactors are commonly used equipment in enterprises. However, the use of any equipment requires a certain understanding of its related knowledge. This will not only reduce equipment failures, but also increase the efficiency of equipment. Therefore, glass-lined reactors In the use of the enamel, the composition of the glaze is the key to the efficiency of the equipment. We need to understand the composition of the composition.
The general composition of the enamel formulation of industrial glass-lined reactors is mainly silica, the content of silica occupies 50%~80% of the enamel surface, the content of boron trioxide is about 12%, sodium oxide At around 12%, cobalt oxide is around 3%. Thus we can see that the enamel of the glass-lined reactor is a glass-like substance formed by mixing a variety of chemical mineral raw materials and chemical raw materials in a certain proportion after melting or semi-melting.
In the production process of enamel and glaze, we can divide its composition into matrix agent, fluxing agent, opacifier, oxidizing agent, coloring agent and auxiliary agent. Not every component plays a single role, sometimes one The substance may be both a base agent and a fluxing agent, for example, boron trioxide is both a base agent and a co-solvent. The composition ratio of the enamel is different, it can form the base glaze and the top glaze. The base glaze is the glaze in which the fired porcelain layer and the steel body are closely combined. The composition ratio increases the content of the adhesive and strengthens the combination of the porcelain layer and the steel body. The composition ratio of the top glaze increases the content of corrosion-resistant components, so that the fired outer enamel layer has high corrosion resistance, and the difference in composition can make the fired enamel layer appear blue. Different colors such as white and white.
According to the different requirements of the firing process temperature, it is divided into high temperature enamel and low temperature enamel. The components of high temperature enamel and low temperature enamel and the firing temperature are different. The advanced components of high temperature enamel require high firing temperature and its physical and chemical properties. Relatively enhanced, thereby improving the stability and corrosion resistance of the glass-lined enamel layer; low-temperature enamel lags behind the composition and requires a lower firing temperature; it is also easy to distinguish from the color of the glass-lined product: high-temperature enamel firing is pure blue While it is bright, the low-temperature enamel fired is blue-black and dark. Because the composition and firing cost of high-temperature enamel are higher than low-temperature enamel, some small factories often choose low-temperature enamel, which is a disguised cut corner, in order to save costs. Please pay attention to the majority of users.
To sum up, according to the description of the composition of the enamel of the glass-lined reactor, the equipment can be used better, and its service life can be effectively extended, thereby promoting the production of the equipment.
Related News
Durable Blade Type Glass Lined Agitator
2025-07-02
Newest K10000l Glass Lined Reactor
2025-06-03